Additive manufacturing is driving a new automotive frontier
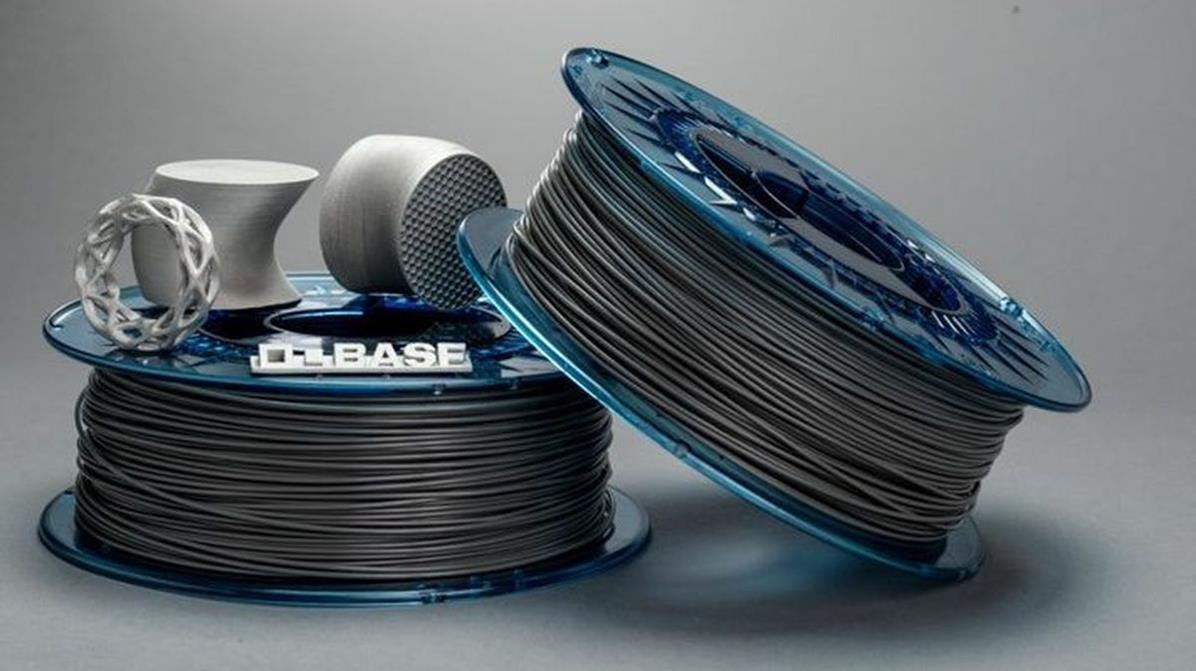
The advent of additive manufacturing has impacted how products are created across industries like aerospace, medical and consumer products. In the automotive industry, additive manufacturing has the potential to advance and transform both vehicle development process and manufacturing. OEMs and suppliers are exploring creative solutions for additive manufacturing beyond rapid prototyping and making use cases for high-volume direct manufacturing in the future.
Unlocking the full potential of additive manufacturing
One of the main benefits of additive manufacturing is increased speed, enabling a more productive process and generating a paradigm shift for the development of tooling and vehicle components. Automotive parts can be designed and made in a matter of days rather than the typical turnaround time of weeks. By including additive manufacturing equipment outside of the design studio and on the factory floor, automakers can create multiple assemblies from one machine to save time and reduce the amount of component inventory on the shelf.
Additive manufacturing also enables greater design freedom and the ability to create complex automotive components. The VisionVenture concept camper is one such example. Co-created with HYMER, BASF 3D printed more than 100 interior and exterior components for the camper. Without additive manufacturing, the cost and complexity of prototyping applications for a custom vehicle like VisionVenture could not be justified. While additive manufacturing now is typically used to create specialty parts for niche vehicles, the goal is to shift the focus to broader applications for large volumes of production vehicles.
Another benefit is reduced cost. By leveraging additive manufacturing, during the design and innovation phase, automakers can reduce the cost of prototyping. Additive manufacturing offers many opportunities to lower costs, such as with on-demand and on-location production, reduced tooling needs, lower inventory levels, among others.
There are also environmental benefits to implementing additive manufacturing. Manufacturing components either onsite or closer to the point of use increases shipping efficiencies and decreases the CO2 footprint. Shorter distance sourcing is more eco-friendly and helps prevent any interruptions along the global supply chain.
When looked at collectively, the benefits of additive manufacturing in automotive has significant potential for OEMs and suppliers to increase competitiveness in an increasingly complex industry.
To accelerate adoption, standardization is a must
Despite the potential, additive manufacturing has yet to reach mass adoption across the automotive industry. Multiple OEMs have set varying specifications, and this lack of standards is hindering the ability for automotive additive manufacturing to scale.
While establishing standards is a huge and complex undertaking, BASF sees this as an area for opportunity. Leveraging our technical expertise and material know-how, BASF is working toward standardization in additive manufacturing.
BASF is already engaging with machine manufacturers to determine standards for a combination of a particular material and particular machine. Addressing each key area separately can help determine some uniformity; for example working with additive machine manufacturers in photopolymers to group a specification, then grouping powder bed or filament developers. It’s important to be consistent, but parts can be designed differently as long as the inputs are known.
Machine manufacturers also construct parts in different ways, changing the topology of how a part is constructed, if it’s layered or not, etc. The mechanisms that suppliers use to create a part, whether it’s a filament disposition, melting or chemical bonding of powders, can determine part sensitivities. Another potential solution is to go by major categories as each type of process has certain weakness, which will drive specifications.
A one-stop AM shop
To gain broader industry acceptance, suppliers like BASF must develop material specifications that perform and are cost effective. On the OEM and Tier 1 customer side, there has to be a known commodity to analytically design with, just like with conventionally constructed parts.
BASF’s Ultrasim virtual engineering software can help with this. Ultrasim characterizes and optimizes the behavior of specific materials in the additive manufacturing process. Through computer-aided engineering (CAE), Ultrasim simulates new ways to reshape a part and shows how to get more out of it than by using traditional techniques, creating designs that are additive manufacturing-ready.
Ultrasim is only one of the tools in BASF’s portfolio. From high-performance printing materials and design thinking to processing solutions, BASF provides comprehensive, tailored services for additive manufacturing applications.