BASF and Casio Computer Company cooperate to reach next level of robustness and performance for digital fitness watches
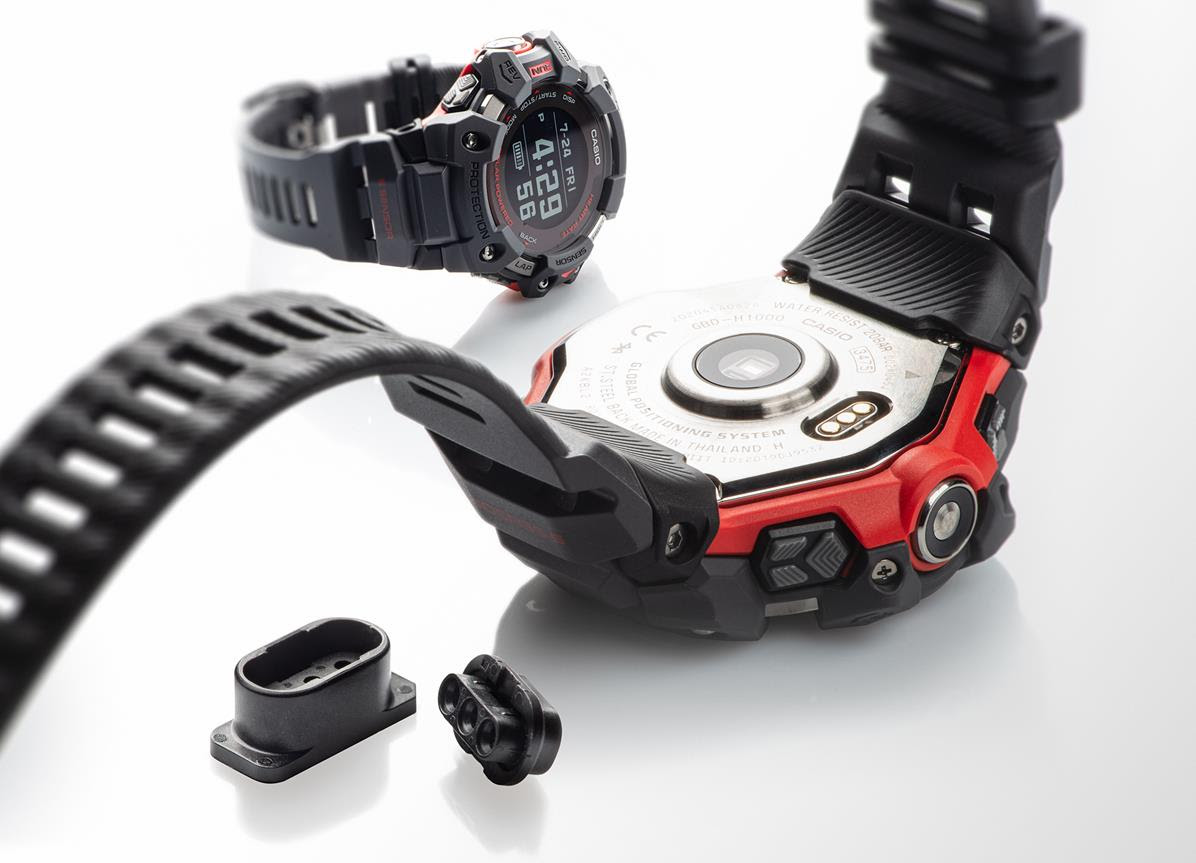
- Latest G-Shock model by Casio made with BASF’s Ultramid® Advanced N results in enhanced durability and exceptional mechanical properties under harsh conditions
- Extremely low moisture uptake and excellent retention of properties at high temperatures of new BASF polyphthalamide ensure dimensional stability during and after Surface Mount Technology
Casio Computer Company, Tokyo, now uses BASF’s high-performance plastic Ultramid® Advanced N in its latest digital watch G-Shock GBD-H1000. The new flame retardant polyphthalamide (PPA) is used to manufacture the terminal header which sits on the terminal block and contributes to power charging and data synchronization. The high heat resistance as well as the exceptional mechanical and dimensional stability of the BASF material enhance the robustness, functionality and performance for which the G-shock watches are renowned. Due to its low moisture uptake and high heat deflection temperature, the BASF PPA is especially suitable for Surface Mount Technology (SMT) processes in electronics manufacturing as it prevents blistering or changes in dimensions of the processed part. With its intrinsic good laser transparency, Ultramid® Advanced N also offers more freedom for post-processing.
The newly launched GBD-H1000 sports watch serves as a fitness tracker with five different sensors. This requires a combination of technologically innovative and durable materials that are resistant to chemicals, shock and water especially during extreme sports. Ultramid® Advanced N displays excellent dimensional stability under humidity and heat as well as exceptional chemical resistance while having good adhesion to the metal terminal block. This prevents water leakage under harsh conditions and fulfills the waterproof requirements of Casio. The part made of the BASF PPA is about 1.2cm wide with a wall thickness of 0.2 mm and weighs less than 0.1 gram: The material thus contributes to downsizing while keeping high mechanical strength.
The successful collaboration between Casio, BASF and the Taiwanese connector company Aces Electronics has not only enhanced Casio’s ultimate tough watch design concept but also increased the speed and efficiency in delivering the right material for the G-Shock GBD-H1000. With the BASF PPA, Casio can make watches more durable while integrating new digital and interactive functions.
“Wearable devices open up new possibilities for consumer electronics companies like Casio. Their users place high demands on them regarding functional integration, usability and design which all result in new challenges for the materials employed,” said Minli Zhao, Vice President, Consumer Industry, BASF Performance Materials Asia Pacific. “BASF has been developing its new generation of innovative, state-of- the-art PPAs under the trade name Ultramid® Advanced so that our customers can stay ahead of the game and users enjoy the latest digital innovations in everyday life.”
The terminal header made of Ultramid® Advanced N was manufactured by Aces Electronics. The terminal block and header are fixed to the motherboard by SMT, which is often applied in electronics manufacturing such as watch assembly today. So a stronger material than usual was required to meet the heat distortion temperature of up to 260°C during the production process using SMT. In extensive tests the BASF PPA proved its superior accuracy and quality during different production processes when compared to other materials currently available on the market.
About Ultramid® Advanced
BASF’s polyphthalamide portfolio is based on the four polymers Ultramid® Advanced N (PA9T), Ultramid® Advanced T1000 (PA6T/6I), Ultramid® Advanced T2000 (PA6T/66) and the long-standing Ultramid® T KR (PA6T/6). They open the door to the next generation of lightweight, high-performance plastic components in many different sectors including the automotive industry, electronics and electric devices, mechanical engineering and consumer goods. The PPA portfolio is available globally and complemented by BASF’s Ultrasim® simulation tool and extensive experience in application development. It includes more than 50 compounded grades for injection molding and extrusion, products with or without flame retardants. The compounds are available in different colors, from colorless to laser-markable black, with short-glass, long-glass or carbon fiber reinforcement, and with various heat stabilizers.
Further information: www.ultramid-advanced-n.basf.com andwww.ppa.basf.com.
About BASF’s Performance Materials division
BASF’s Performance Materials division encompasses the entire materials’ know-how of BASF regarding innovative, customized plastics under one roof. Globally active in four major industry sectors – transportation, construction, industrial applications and consumer goods – the division has a strong portfolio of products and services combined with deep understanding of application-oriented system solutions. Key drivers of profitability and growth are our close collaboration with customers and a clear focus on solutions. Strong capabilities in R&D provide the basis to develop innovative products and applications. In 2019, the Performance Materials division achieved global sales of €6.06 bn. More information online: www.plastics.basf.com.
About BASF
At BASF, we create chemistry for a sustainable future. We combine economic success with environmental protection and social responsibility. More than 117,000 employees in the BASF Group work on contributing to the success of our customers in nearly all sectors and almost every country in the world. Our portfolio is organized into six segments: Chemicals, Materials, Industrial Solutions, Surface Technologies, Nutrition & Care and Agricultural Solutions. BASF generated sales of €59 billion in 2019. BASF shares are traded on the stock exchange in Frankfurt (BAS) and as American Depositary Receipts (BASFY) in the U.S. Further information at www.basf.com.Download Media