HYBRIT: A unique hydrogen storage facility in Luleå is taking shape
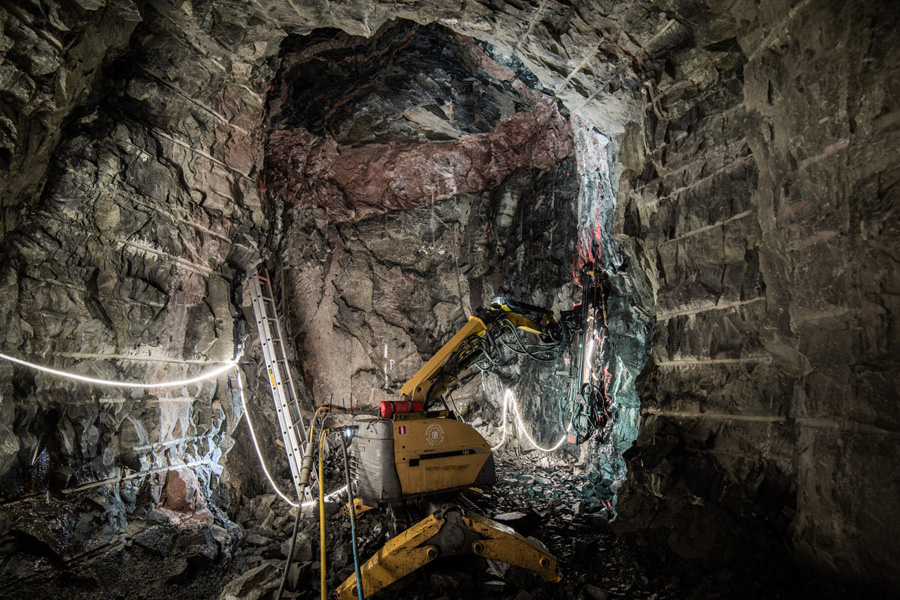
Construction of the rock cavern storage facility for fossil-free hydrogen in Luleå has reached the halfway point. Right now the steel lining is being installed inside Svartöberget. The storage facility, which will be an important part of the value chain for fossil-free iron and steel production, is planned to be in operation by the summer.
The HYBRIT initiative was launched in 2016 by the three owners; SSAB, LKAB and Vattenfall. The hydrogen storage facility will play a very important role in the overall value chain for fossil-free iron and steel production. Production can take place without a storage facility, but storage provides the opportunity to vary the demand for electricity and ensure stable production. By producing hydrogen gas when there is a lot of electricity, for example when there is a lot of wind, and using stored hydrogen gas when the electricity system is under strain, will ensure production.
“The hydrogen storage facility has a stabilising effect on the electrical system. It reduces the risk of the system overloading. We want to develop HYBRIT technology so that it is in line with the future electricity system with more weather-dependent electricity generation,” says Mikael Nordlander, Development Manager for Vattenfall’s industrial partnerships.
Proven technology
The storage facility is unique and once again the HYBRIT initiative is taking the lead in the fossil-free transition. The technology for storing gas in a lined rock cavern (LRC) is well proven and has been used in southern Sweden for about 20 years for storing natural gas. However, the technology is now taking another step forward as it’s being developed for the first time with hydrogen gas on a large pilot scale.
“What’s so fantastic about HYBRIT is just how many different innovative parts the initiative consists of. The hydrogen storage facility is a good example of how we’re testing and using innovations to achieve the goal of a completely fossil-free value chain, the first in the world,” says Martin Pei, Technical Director at SSAB.
“The hydrogen atom and the hydrogen gas molecule are the smallest that exist, which brings special challenges. We want to see that the storage facility can cope with variations in pressure and can keep up when electricity generation varies,” says Susanne Rostmark, research leader at LKAB.
The various parts of the plant are now mostly in place. Rock caverns and connecting tunnels have been constructed in the rock and a ventilation shaft has been drilled from the top of the rock down to the upper part of the rock cavern. At the end of 2021, the compressor that will be used to pressurise the hydrogen gas for storage was lifted into place.
Intensive work in progress
Since the start of construction, the pipelines needed to transport hydrogen gas to the storage facility have also been put in place. The hydrogen gas that will be stored is being produced in connection with the pilot plant for fossil free steel production by means of direct reduction that is already in operation in Luleå. The hydrogen can be used both in the direct reduction trials and in the storage tests.
“Intensive work is under way at the moment to complete and inspect all installations, while the facility’s steel lining is being welded together in the cavern,” says Mikael Nordlander.
Using HYBRIT technology, SSAB, LKAB and Vattenfall can help reduce Sweden’s carbon dioxide emissions by 10 per cent and Finland’s by 7 per cent. Fossil-free hydrogen gas instead of coal and coke is crucial to the HYBRIT technology.
The owners SSAB, LKAB and Vattenfall are investing a total of around SEK 200 million in three equal parts, and the Swedish Energy Agency is contributing just over SEK 52 million to the construction of a fossil-free hydrogen storage facility.
Facts about the hydrogen storage facility
- Construction of the hydrogen storage facility began in May 2021 and the plan is for the plant to come into operation during the summer of 2022. The tests will then continue until 2024.
- Hydrogen storage will be tested in the storage facility using known technology known as LRC (Lined Rock Cavern).
- The fossil-free hydrogen (green hydrogen) is produced by water electrolysis using fossil-free electricity.
- It’s important to build in rock of a type that maintains its good qualities. For example, the bedrock in Svartöberget consists mainly of amphibolite with elements of pegmatite and red granite.
- The storage facility is a pilot plant measuring 100 cubic metres and will contain hydrogen gas pressurised up to 250 bar. At full scale, potentially 100,000–120,000 m3 storing 100 GWh of electricity converted to hydrogen, it will be enough to power a full-size steel mill for about three to four days.
- The rock cavern where the gas is stored is located about 30 metres from ground level, and the distance from the opening for the connecting tunnels to the rock cavern is about 100 metres.
Facts about the HYBRIT project
- The HYBRIT initiative was launched in 2016 by the three owners; SSAB, LKAB and Vattenfall.
- With the HYBRIT initiative, SSAB, LKAB and Vattenfall intend to create a completely fossil-free value chain from mine to finished steel, with fossil-free pellets, fossil-free electricity and hydrogen.
- The pilot facility for the production of fossil-free sponge iron in Luleå was commissioned on 31 August 2020.
- On 24 March 2021, Gällivare was chosen as the location for the planned demonstration facility for industrial scale production. Sponge iron is used to make steel.
- In May 2021, construction commenced of a storage facility for fossil-free hydrogen gas on a pilot scale next to HYBRIT’s pilot facility for direct reduction in Luleå.
- In August 2021, SSAB produced the world’s first fossil-free steel, produced using HYBRIT technology, and delivered to the customer. The test delivery was an important step toward a completely fossil-free value chain for iron and steel production and a milestone for the HYBRIT collaboration between SSAB, LKAB and Vattenfall.
- Hybrit Development AB is a research and technology development company that will deliver solutions to the plants. Technological development will take place in close partnership with the holding companies.
- The steel industry today accounts for 7 percent of total global carbon dioxide emissions. Using HYBRIT technology, SSAB, LKAB and Vattenfall can help reduce Sweden’s carbon dioxide emissions by 10 per cent and Finland’s by 7 per cent.
- Fossil-free iron and steel production using HYBRIT technology, corresponding to SSAB’s current production level, will require approximately 15 TWh per year. This will require permit granting processes to be faster and easier to acquire for the expansion of Sweden’s electricity network and generation.