Innovation in Motion: Singapore’s battle against Covid−19
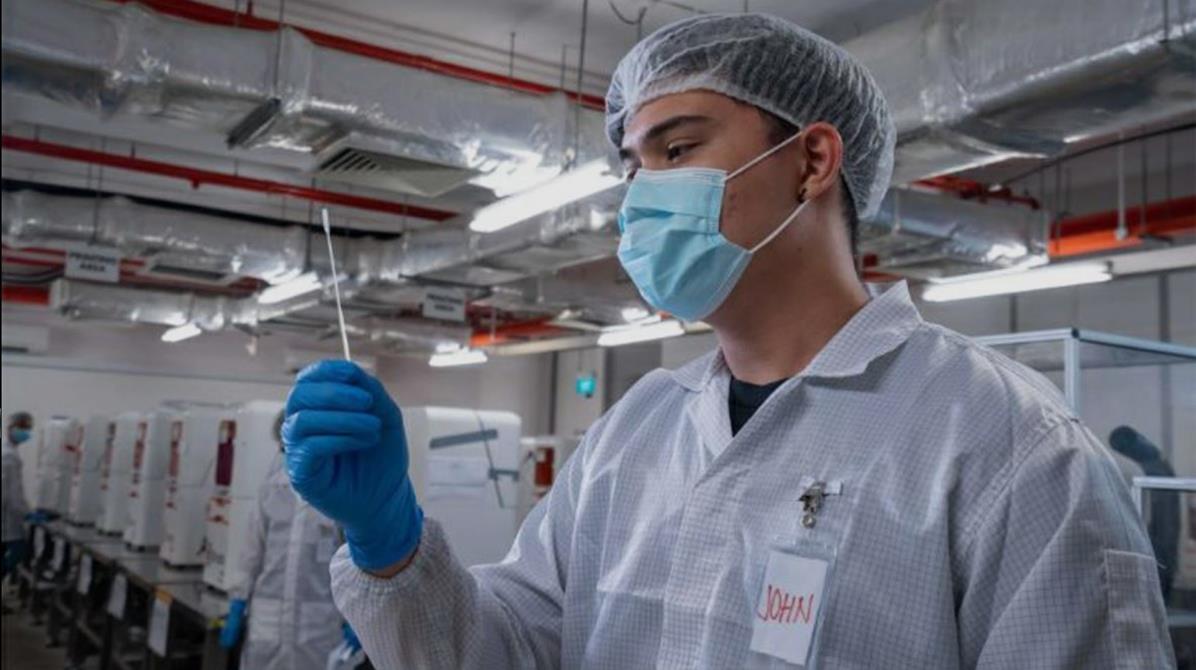
Faced with a global shortage amid the COVID-19 pandemic, a multidisciplinary research team in Singapore innovated a new method of producing nasopharyngeal (NP) swabs in less than seven weeks, enabling the city-state to curtail an uptick in infections.
The shortage of NP swabs was among the biggest challenges the city-state faced amid the pandemic. These flexible bristle-headed sticks are used to collect fluid samples from the nose and throat. Without them, testing for the virus is not feasible, yet the limited number of manufacturers worldwide were unable to meet the sharp spike in global demand.
“There were two choices,” said Andrew Tan, Managing Director at Temasek’s Enterprise Development Group, part of the Singapore state sovereign fund that identifies and develops new business enterprises that have the potential to be domestic, regional or global champions. “Find alternative sources or produce them locally. We decided to do both. We continued sourcing commercial swab kits, diversifying the number of suppliers. And more importantly, we built up local capabilities to produce them.”
Rising to the Challenge
Building local production capacity was a daunting challenge. NP swabs are regulated, patented and highly specialized. They cannot be produced on the fly, thus a diverse team of experts was much needed. Temasek quickly assembled a team of 3D printing experts, industrial designers, test certification professionals and infectious disease specialists to overcome the challenge.
Using 3D printing, the multidisciplinary team circumvented the months-long mold fabrication and tooling qualification that traditional production requires. It took them less than seven weeks, working around the clock to iterate and validate more than 30 designs, before shortlisting two designs for patient trials.
Working closely with infectious disease experts and Ear, Nose and Throat specialists, the team closed in on the design featuring a double helix tip. Called Python, the selected swab design demonstrated comparable accuracy and performance to the industry standard FLOQswab during patient trials.
“Technical challenges aside, the main challenge we faced was one of changing mindsets,” said Temasek’s Andrew. “It was a question of getting the wider medical community to accept the use of novel 3D swabs following successful clinical trials, given that many of them were accustomed to using commercial swabs. We also tried the swabs on members of our own team as well, as providing samples for the local clinicians to use. Eventually, they came around.”
Ramping Up Production
With a patient-ready design in hand, two local 3D printing companies began mass production in early June. Both had to pivot as neither company had printed an NP swab before the pandemic.
Success required obtaining a large amount of equipment to put the machine capacity in place, securing sufficient raw materials to meet demand and ensuring printing was conducted in a controlled environment. They worked diligently to put the piece in place and have collectively manufactured nearly 5 million Python swabs as of early September.
Besides 3D-printed swabs, Temasek also supported the development of two injection molding (IM) swabs. IM swabs can be produced at a larger scale with a lower cost, but take a much longer time to start production due to the molding and tooling processes involved. IM swab production commenced about three months after Python’s started production.
By year-end, Singapore will have produced some 20 million swabs using the 3D printing and IM production processes. To facilitate more broad-based testing, Temasek is now also exploring new testing methods, including saliva-based tests and needle pricks.